Rieger Custom tip machine pattern #60 is now available
- ericarbiter
- Feb 18, 2022
- 5 min read
Updated: Apr 5, 2022
To the readers of my book, The Way of Cane, or anyone else interested, I want to announce that Georg Rieger now has my custom pattern available. It is tip profiler pattern #60.
In this photo, the narrow spine that characterizes this pattern is visible.

It is especially easy if to change out of you have a tip machine made after 2014 since the patterns can easily be changed without taking the machine apart to replace the whole pattern block. If bassoonists have earlier machines, as I do, it is possible to convert the machine to the new design by adding the part# F3S1100 which is the base plate that accepts the interchangeable patterns. Those not feeling comfortable performing the changeover can send their machines to Rieger, or I can do the conversion though The Way of Cane, bassoon reed machine service. Send me a message or e-mail.
Here are shadow photographs of reeds made from the replica of the pattern I had Georg Rieger make for me in 2004. The new replica pattern produced by Johann Rieger is identical to my original.

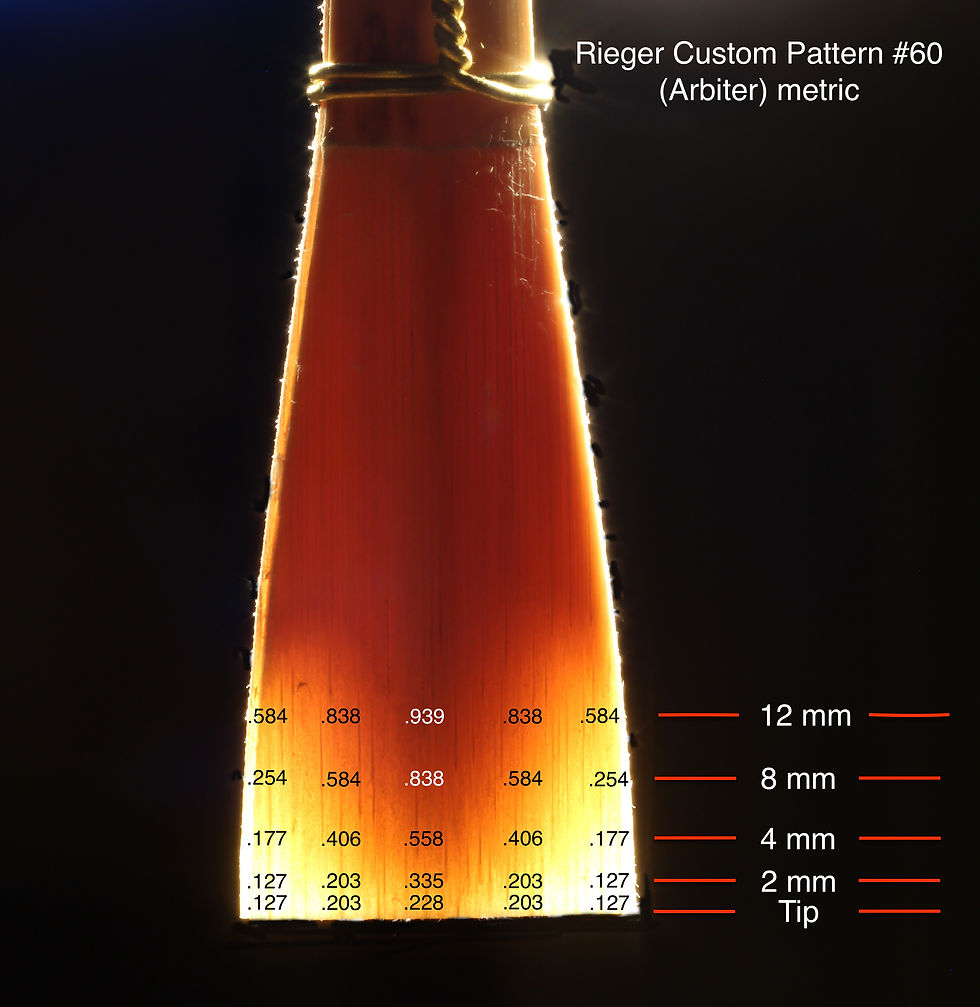
I discuss the history of this pattern in the Way of Cane. Here are page numbers for other shadow photographs of this particular trim type, similar to these except they are in black and white.
Pages xxv, p. 22, p.73, 92, 111, 172-173, 235 (with thickness measurements), p. 305, Bernard Garfield’s reed.
There are so many different ways to trim the bassoon reed. This particular style is the one that works best for me and my bassoon. It’s also one of the reasons that I wrote The Way of Cane: to sketch out some of the major types of trim styles to try if looking for alternatives for directions for possible improvement.
For anyone more interested in the development and history of this pattern I outline it below. It may be too much information—
I found the reed style that made a big difference for me with my month of lessons with Bernard Garfield during my winter term in 1969, my first year at Oberlin Conservatory. I immediately took to his reeds and began to model mine after this style. In those days, reed machines were much simpler so most of the work had to be done by hand.
Fast-forward several years later to 1974 when I started my position of Associate Principal in the Houston Symphony. During my first year, I was having problems playing 3rd bassoon (low and very softly) when the repertory required it. My bassoon was leaking a lot— or my reed making just wasn’t up to the task– but for whatever the reason, I needed help.
I read in To The World’s Bassoonists by Gerald Corey, a recommendation for reeds made by Walter Urbach, who performed in the Berlin and Nuremberg Philharmonic Orchestras, and I ordered four reeds which worked very well for me. Coincidentally these reeds were constructed along similar lines to Mr. Garfield’s so it was a win-win for me and solved my problems until I could get my bassoon sealed properly. I continued to use both the Urbach and Garfield reeds as models for my own.
Although Mr. Garfield made a reed for me at one of my lessons, it remained on the drying rack while the binding glue was drying and we both forgot for me to take it after my lesson. I never had one of his reeds for my study. He trimmed on the reeds I brought to my lessons.
In 1999 one of my colleagues was trying out a Rieger tip profiling machine and offered to let me try it. I could immediately see the great advantage of this machine so ordered one from Bob Williams (principal bassoonist of the Detroit Symphony) who was a distributor for Rieger. I was delighted with the machine, although it didn’t have a tip pattern quite like the one I was making by hand. So I slightly modified the pattern using thin layers of tape to build up thickness in the pattern where I wanted it; this worked well. The tape would gradually wear out but was easily replaceable and this gave me the result I was happy with.
A few years after that, I discovered that Rieger could make a custom pattern block from finished reeds so I decided to send him some sample reeds which were based on my adaptation of the reeds made by both Urbach and Garfield that worked for me in the orchestra’s large concert hall. I often wondered whether Walter Urbach had a Rieger tip machine back that far, while Georg Rieger was still working as a master machinist for Mercedes. See:
It looked to me like he may have since all the reeds he sent me were amazingly consistent.
I received a confirmation from my friend and excellent reed maker, Rick Yoder (London Fields Reed Shack: http://www.londonfieldsreedshack.com/index.html ) about Walter Urbach’s use of the Rieger tip profiler as far back as 1972. He even included a photo of Urbach's machine. Rick studied with Urbach when he was in Germany.
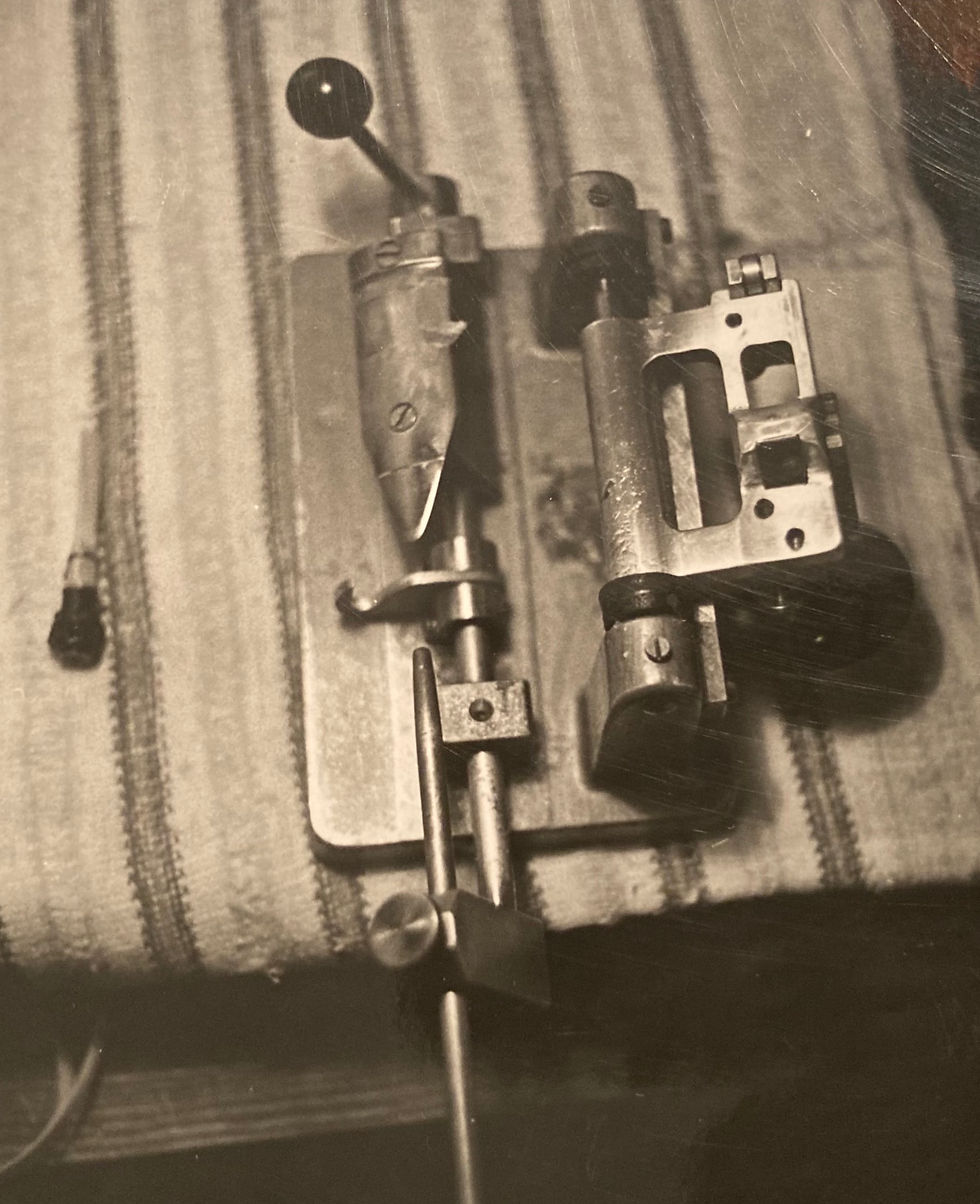
Walter Urbach's Rieger tip profiler
I was satisfied just having this pattern for myself until I completed The Way of Cane, at which point I wondered whether anyone else might be interested trying the pattern. I think it is a fairly unusual trim, at least in America.
Concurrently, my friend Roger Tropman, whom I met during my graduate school days in Cleveland, became increasingly interested in making his own reeds and I was happy to help. Roger encouraged me to write a book on reed making about 12 years ago, which summarized some of my reed ideas that we talked about on the phone over many years ( the impetus to write The Way of Cane). He is a retired middle school band director and excellent amateur bassoonist. In his retirement he is the proprietor of Nexus Woodwind Supply:
I highly recommend his tools for reed making, some of them we have designed together.
Since Roger found that the style of reed I was making worked well for him, too, he wanted to have the same machinery that I used. That meant using my pattern for the Rieger tip machine, but unfortunately Rieger didn’t keep the data he used to make it. This began about 4 years ago. That started our project to get a copy made for Roger. Ideally, Johann Rieger advised sending my original custom pattern block back to him to measure, but I wasn’t comfortable having it mailed off and possibly getting lost (paranoid, I know!) and I was still at that point playing in the Houston Symphony (before my retirement in 2019) so I needed my tip machine. Because of that, project languished until this year. Still paranoid about sending my pattern off, I ended up mailing Johann several tip-finished reeds to measure. I must say he did an outstanding job transferring the data from these reeds to the finished new pattern, Rieger #60. I tested and compared many blanks made on both my original custom pattern and the new one and they seem the same to me both in terms of measurements and how the reeds play coming off the tip machine.
I am also working with Udo Heng of Reeds ‘n Stuff to make a replica pattern for his excellent tip machine. I’ll post when that becomes a reality.
Anyone interested in this pattern should get in touch with Silke at Rieger who has been most helpful in shepherding this project through to completion:
For anyone who decides to try this pattern, I would recommend also adjusting the main profile to leave the front third of the reed heavy enough to not preempt the spine that characterizes this pattern. For me that means the thickness at the fold should be around .025” (.635 mm). This will allow the pattern’s spine to be utilized up at the front of the blank.
In a future post I will talk about my method of setting up a tip machine with a new pattern.
Thank you for this post. I saw your pattern on the Rieger website and became interested because it has a narrower spine compare to the others. however, I was quite surprised to see how heavy your measurements actually are at the tip of the reed. The thickness at 8 mm from the tip of your pattern is pretty much as heavy as the very back of my reeds, which is 0.33''. I am very curious about the measurement you have for the back of your reeds. Thanks!